The product must also reach the heart.
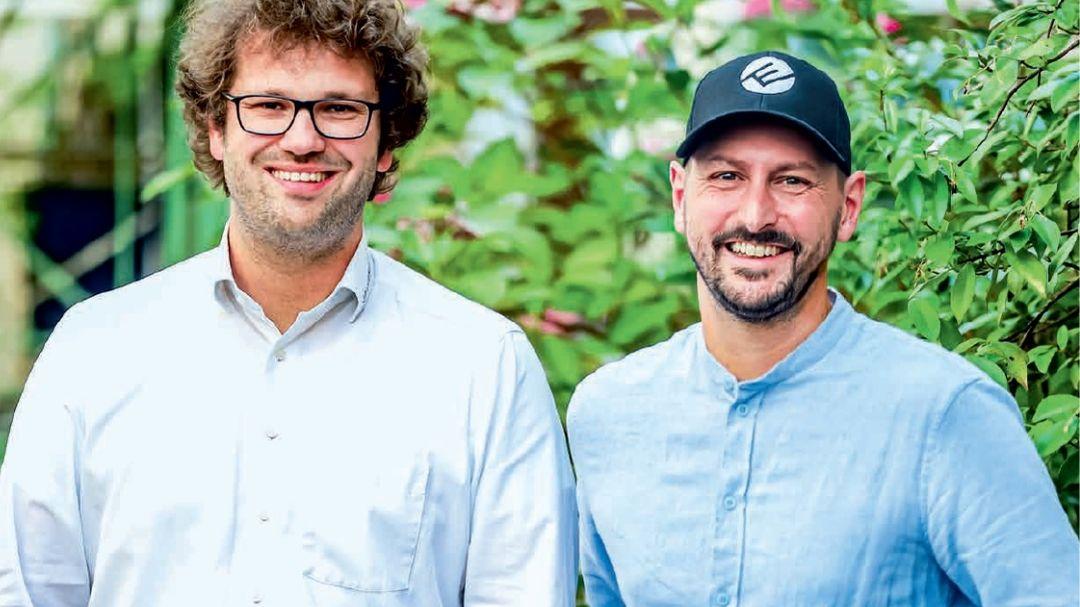
They didn't promise too much: Stefan Becker and Benjamin Neubauer's office is actually located in a picturesque backyard in the middle of Munich - it could also be Master Eder's workshop and Pumuckl's prankster. In fact, a lot of new ideas are conceived and implemented here. It is from here that the two EVOMECS managing directors and their team develop and manage their software solution, which is designed to help companies in the tool and mold making industry to simplify all processes.
Stefan, you have a doctorate in physics and grew up in a tool and mold making company. How did you come up with the EVOMECS idea?
In 2008, my father wanted to improve the process after a machine crash and make sure that something like this didn't happen again. A communication problem was identified as the cause of the error. However, there was nothing tangible that would have helped to improve the process. So he asked me what it takes to learn from mistakes in single-part production. This question fascinated me.
And the answer is ...
You have to be able to organize the processes in such a way that activities can be carried out under individual responsibility. So when someone carries out a work step, they shouldn't have to ask anyone. It therefore makes sense to digitally map production across all process steps. This then opens up enormous potential for rationalization. If production is digitalized throughout, this means that much less knowledge has to be reproduced in the individual work steps. For example: someone reads something and types it into the control system, i.e. uses information that has already been created in another work step and rechews it again for the next work step. This takes longer, requires a person and therefore harbors the risk of errors. However, if production is mapped across processes, all of this can be eliminated.
So that's what EVOMECS is all about?
Yes, it is an end-to-end digitalization system with access to everything that can be digitally connected in a meaningful way, such as machines, handling, CAM or storage systems. Your first customer was Dast. How did development continue from there? We introduced the process control technology from Zwicker Systems at Dast in 2010. However, Zwicker filed for bankruptcy in 2012. At that time, I realized that a digitally integrated system was relevant for the entire industry and that such an application had to be built with new technology - that was the birth of EVOMECS. In 2013, we initiated developments in this direction and got the first version up and running at Dast in 2016...
... for milling machines. Was the design of the application already open enough back then to be able to integrate EDM machines or other devices, for example?
When designing such a system, the trick is to build it technically in such a way that it has the longest possible life cycle. From the very first step, we tried to ensure expandability. The entire area of quality management was also part of EVOMECS very early on. In 2016, however, the system was still designed for milling, but we introduced the Kanban concept in version 2 in 2019 and significantly generalized this system for version 3. Users can now also plan and schedule resources, i.e. map complete projects - with purchasing, parts handling, dependency analysis and planning. We are currently in the process of integrating assembly instructions into the system.
Benjamin, it certainly takes missionary zeal to get a toolmaker who is involved in day-to-day business to invest in a virtual product like EVOMECS.
Of course, there are companies that immediately think of a new machine when they think of optimization. But for us, it's about processes. It's about the way you do things and how you deploy your skilled workers. This is initially something abstract that cannot easily be visualized, but it also holds potential that is actually still completely untapped.
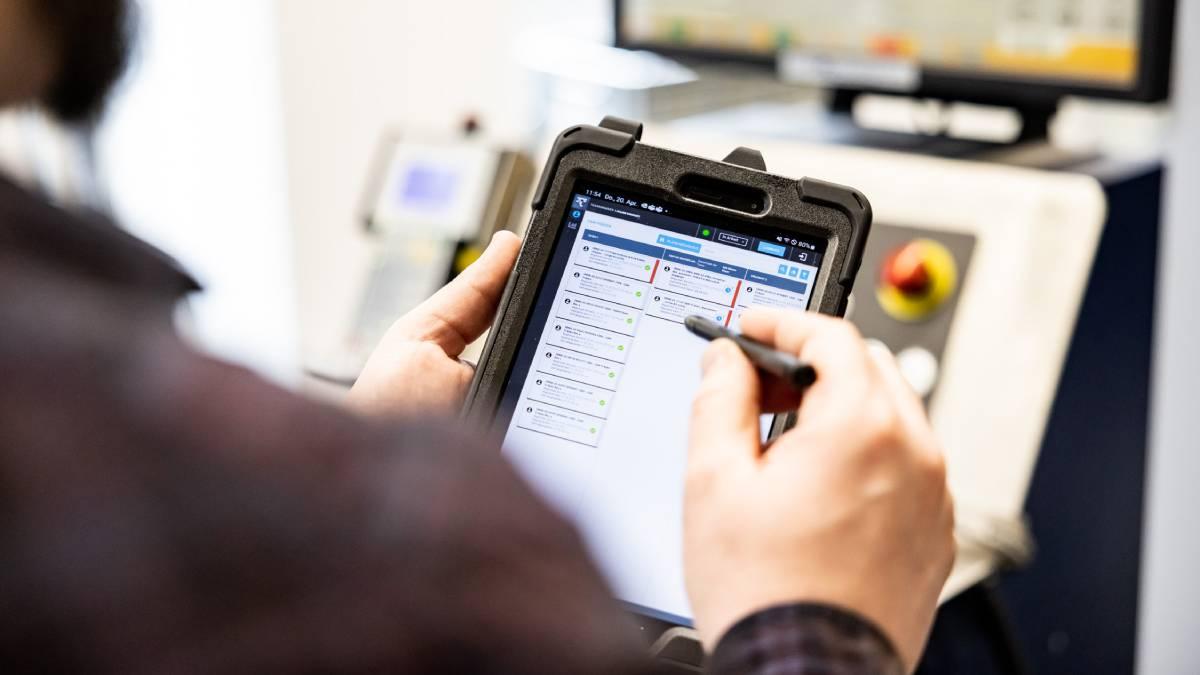
You sell software with an attitude behind it. How do you communicate the content of EVOMECS?
Up to now, we have visited prospective customers at a reference customer, followed by a workshop in which we presented a vision of what the future of the company could look like. However, we have found that toolmakers sometimes want to get to the point more quickly, that they want to solve a problem "now" ... Thanks to technological innovations such as cloud applications, potential customers can now simply create a test account and try out EVOMECS for themselves and operate it as a rental solution without any significant investment.
Does it work according to the plug-and-play principle or do I need your expertise as a user?
Setting up the system works in the same way as with classic cloud systems. You register and are first presented with an empty system. You can display dummy data and play around with it. However, we then also have the option of actually operating specific job management and cell control with quick access from the cloud. At the moment, however, companies still need us to do this. But we are currently creating videos and training materials so that companies with technically ambitious employees can set up such a system themselves. EVOMECS is also a purely standard system. There is not a single customer-specific function in it. They all use the same software.
Stefan, what is the biggest concrete benefit for users of EVOMECS?
First of all, it's mainly about rationalization. Especially in tool and mold making, there is a lot of potential to free skilled workers from pointless, non-value-adding activities. However, this only works if the individual production steps are integrated consistently and across processes. We integrate this in various components, for example in the machine connection, tool management or the task manager. We simply want to give companies the options they need to take a step into the future. SMEs in particular need to be able to purchase such a system and operate it without a great deal of effort. We simply want to reach the heart of the user ... But this is only possible if, for example, further developments can be tested easily and reliably. A special technical feature of EVOMECS is therefore that - despite its consistency - each component can be upgraded and downgraded independently of one another.
And EVOMECS is platform-independent. This means that you are in constant contact with machine and control system manufacturers.
We have a very good exchange with both. This comes about through customer projects. A toolmaker wants a specific connection and we then approach the relevant machine or control system manufacturers together. This has worked very well so far. However, there is also a lot of really good hardware in companies where the manufacturer's software is no longer updated. We can offer "retrofitting", which works particularly well for control systems in automation.
Benjamin, how many EVOMECS applications are currently on the market?
About 15, but so far we have been in the development phase. In such a complex technical environment, this can take several years. However, our system is now in a state where we can meet demand very quickly and easily. It is scalable and that is why we are now entering the growth phase.
EVOMECS has therefore been completed at exactly the right time, now that the structural change in tool and mold making is imminent ...
In 2015, our focus was still on topics such as automation and rationalization - and how to teach this to employees in the company. Today, the question is the opposite: where do I get employees from? These are external factors that play into the hands of our offer.
Does EVOMECS also work for other sectors?
Absolutely. We currently have projects in the early stages of mechanical engineering, contract manufacturing and production. We have a very high development speed here because we have designed the core of the system with so much thought. The fact that we come from the tool and mold making industry is of course also an advantage, because we had to drill the technically "thickest board" right at the beginning:
When people in the industry talk about collaboration, standardization is mentioned as an important basis. You also advertise with the term "shared manufacturing". What does this mean?
In the future, companies will be able to share their production orders as easily as they do today with a document or a deadline. If you have an order that consists of different items but don't have the resources to do everything yourself at the moment, the work is simply shared at the touch of a button. If the partner company is not already using Evomecs itself, a system is created in the cloud and everyone involved can continue working on the production order with little effort. All information about the project is then available and the progress of processing can be called up transparently at any time. Although it is an essential part of our concept that the companies are connected via the cloud, the system also works if the data is located on site at the companies. We will therefore always offer the "on-premise" version as well. Collaborative working is not affected by this. You can simply move the system, take all the data from the cloud, install it locally and continue working seamlessly.
Stefan, what are the next steps?
When you start exploring the possibilities of digitalization, hunger comes with food. Our customers take the first step and then often have ideas about what else could be improved with the system. For example, production planning was actually added quite unplanned. We initially regarded it as a problem that had already been solved and that other software systems were taking care of. But then the first users convinced us that it makes perfect sense to carry out planning with the real-time data and the entire context available in EVOMECS. This massively reduces the implementation and maintenance costs of planning systems.
That's part of production planning.
This also opens the door to assembly, which should also be viewed digitally as a work step. We basically categorize what we consistently map into technologies - milling, eroding, measuring, washing, etc. - and assembly is simply another technology. Assembly is simply another technology that is being introduced. Of course, this is much easier to implement via the cloud than a machine connection.
Why is that?
In assembly, it doesn't matter if the internet connection is briefly interrupted. However, in order to continue the production of a machine securely via the cloud, there are a few criteria to consider ...
When humans are involved, this always means a greater source of error.
That is true. But if you give people clear instructions and link their work to a commitment, then you have more opportunities to improve the assembly process. For example, if there are complaints and the history is available digitally, it is much easier to make improvements. Our principle of seamless tracking continues here in assembly.
Benjamin, what's next from a development perspective?
An interesting hype in recent years has of course been the topic of AI. We are currently experimenting with this. In production, we have an incredible wealth of high-quality data. We know all the correlations and statuses. This opens up interesting use cases: For example, if the system in tool management identifies a milling cutter that is damaged, it can automatically check which workpieces have been machined with it. This can prevent faulty components from being delivered.
Are you actually proud of Evomecs?
The field we work in is extremely complex and we are aware that we have a very high level of responsibility towards our customers. However, we are proud that our knowledge and innovations also enable efficient production and therefore prosperity elsewhere, while also supporting sustainability.
Is that what drives you?
SMEs have shaped us. We want the many SMEs in tool and mould making to benefit from the opportunities offered by digitalization.
Large corporations also have the goal of improving processes ...
That's true. Our biggest customer has 10,000 employees. Not all of them work with EVOMECS, but the company has large corporate structures in which our system works just as well.
Is internationalization a goal of EVOMECS?
Absolutely. The application currently runs in the system languages German, English and Polish. But if a user needs Croatian next week, they will get it next week too. You are not a completely virtual network of programmers, but have a permanent office.
Is that important for your work or your appearance?
The office is part of our identity. Distributed working from home works very well for us, but it's just as important to meet up again and again to exchange ideas. We also appreciate the "Meister Eder" character of our office! This is also something that connects us to the SME sector.
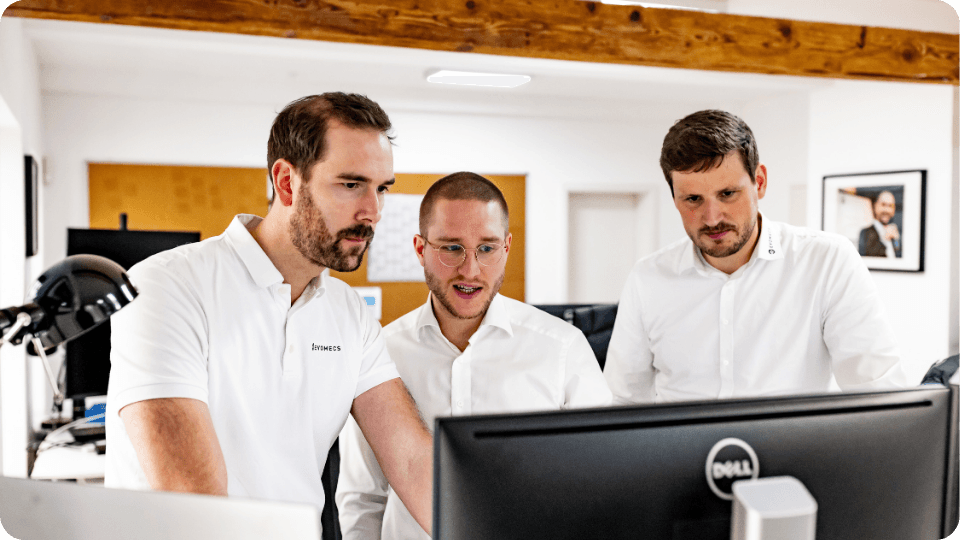
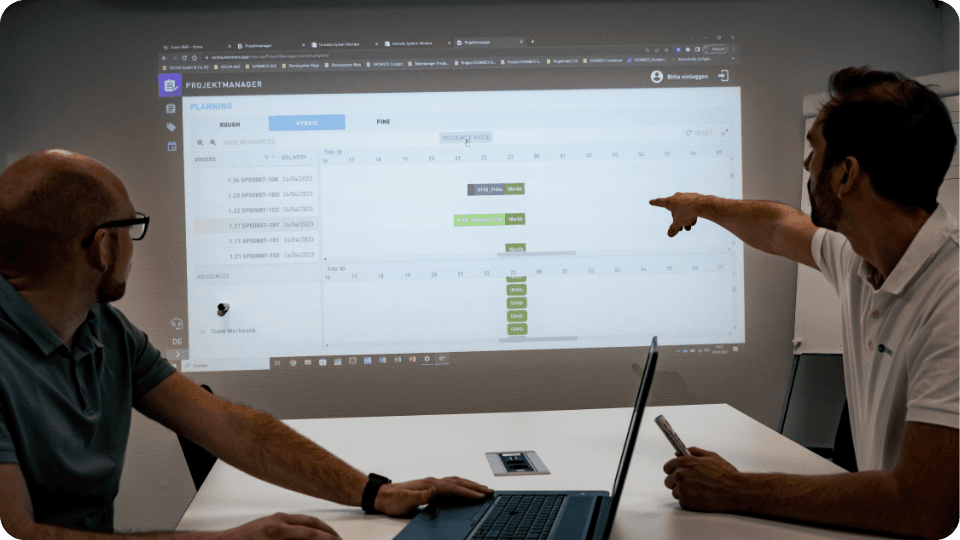
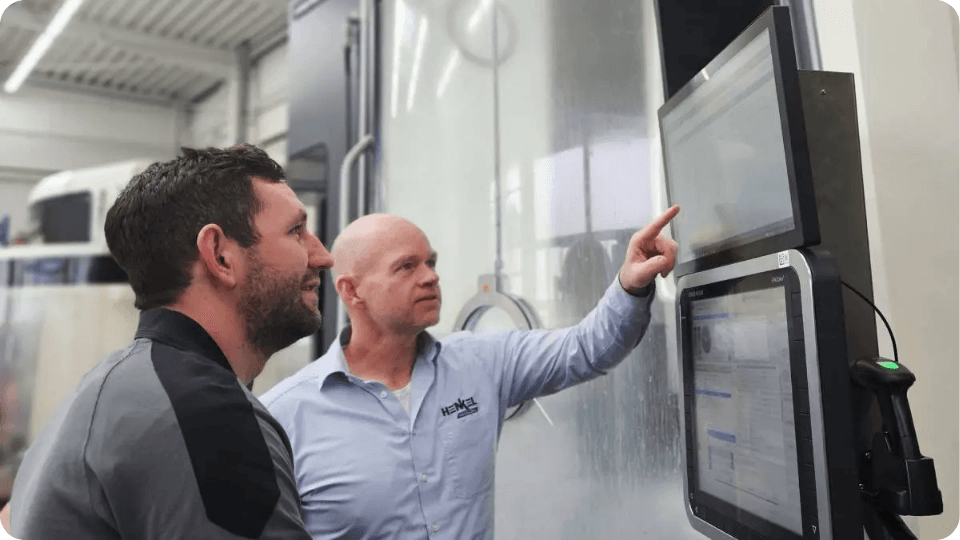