Operate processing machines reliably.
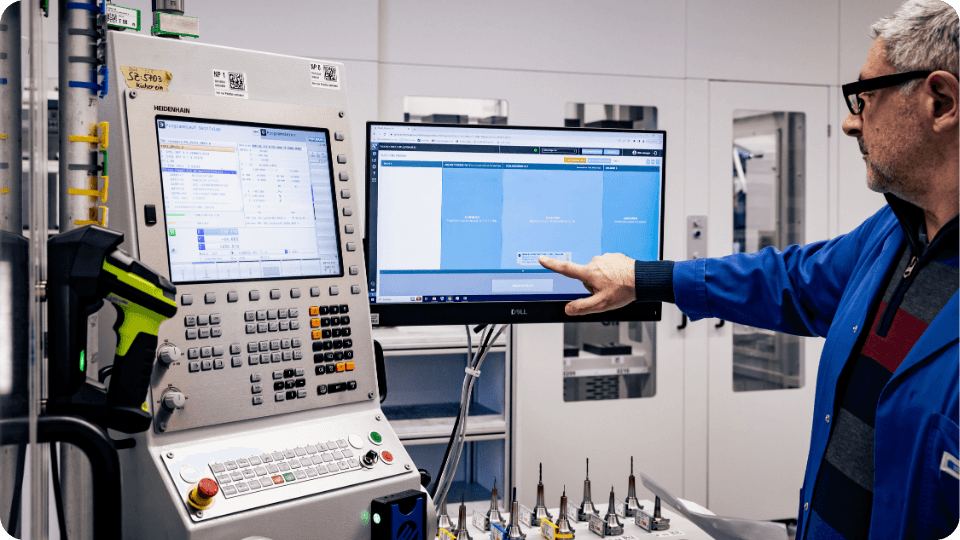
In principle, operating processing machines means operating with large values and a high potential for damage. With its integrated approach, EVOMECS takes over as much of the machine configuration as possible in order to relieve the machine operator as much as possible and rule out possible incorrect entries. These configuration and input requirements for the reliable operation of processing machines, whether in standalone operation or as a cell, include
Job information
It must always be clear which order is to be processed at which machine at which time. Job planning is a highly dynamic process that is generally subject to constant change, particularly in the area of single-part or small batch production.
Process information/NC program
The information about the machine's production process is created in the CAM system and is transferred to the machine via the NC program. It is not only the pure machine-readable code (i.e. the NC program itself) that is important, but also additional process information. For example, fits must be declared for certain workpieces, which the worker must measure and, if necessary, rework on the machine.
Tool requirements
As a rule, a wide variety of consecutive tools are required in the machining program. These tools must be provided in the correct number for machining with sufficient remaining tool life and their exact measurement data must be transferred to the machine.
Workpiece
The workpiece to be machined must be provided in good time and correctly mounted on the machine, either directly or using pre-assembled clamping devices. Here, too, the exact offset data must be transmitted to the machine.
All in all, a large number of input requirements must be met and data and information provided in order to operate a processing machine efficiently and reliably. Small errors in the machine configuration (e.g. incorrectly entered tool measurement data) can cause considerable damage. This means that operating a processing machine generally requires a high level of specialist knowledge, experience and care. In times of an increasing shortage of skilled workers, this is becoming a challenge for production companies that should not be underestimated.
The digital integration of all input requirements, on the other hand, enables significant rationalization potential and an enormous increase in process reliability while at the same time minimizing the technical requirements for machine operators. Highly qualified personnel, on the other hand, can be deployed where the leverage is greatest: at the start of the process.
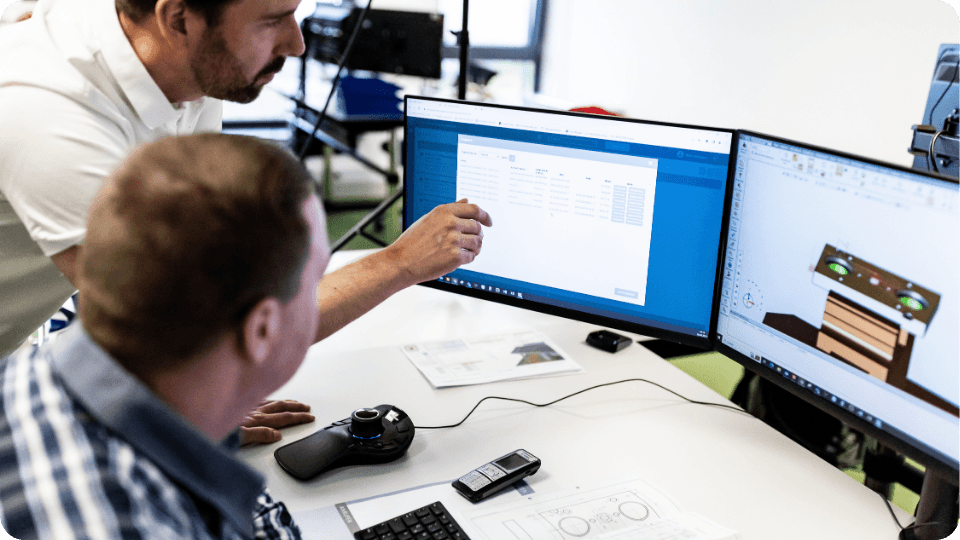
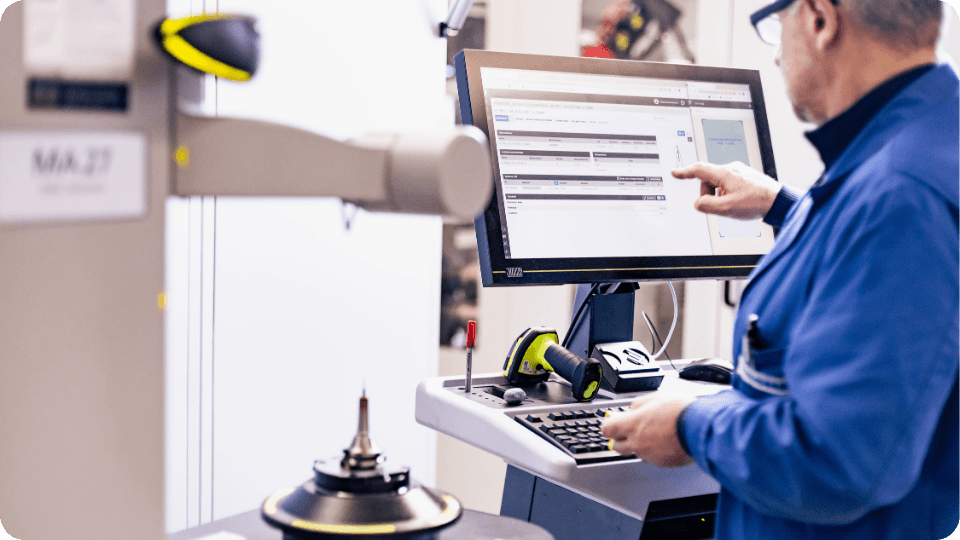
The combination of the EVOMECS MES and tool management components creates the necessary basis for the job management operation of processing machines or cells.
Job information
The job information and the production workflow can be taken from the ERP system as described above, but can also be created and refined in EVOMECS itself. Furthermore, as described, work steps ("tasks") are assigned to specific resources or resource pools, in this case machines or machine pools. These machine work steps can be enriched with QM characteristics, acceptance criteria or other attachments. The release status of the tasks to be processed is also relevant and can be defined. In particular, NC programs can be attached to machine tasks.
Process information/NC program
The CAM programmer outputs his NC program and uploads it to EVOMECS or attaches it to the corresponding task. There are various expansion stages for processing the NC program.
- Level "Automation"
In the "Automation" expansion stage, the NC program is received and only the tool information is read out. Otherwise, the NC program is only transferred to the machine as a "black box" via the corresponding task. The tool information read out can be used to determine tool requirements, initiate the procurement process and check tool availability on the machine. - Level "Full"
In the "Full" configuration level, the CAM programmer outputs the NC program in simple Heidenhain plain text format. When uploaded to EVOMECS, the NC program is converted into its own machine-independent format and fully analyzed. This enables extensive automation and predefinition of the machining process by the CAM programmer, such as sister tool management, tool difference lists, automated fit handling or planned interventions by the machine operator.
Tool requirements
The tool requirements for a component to be manufactured are derived from the NC program, as the NC program is stored in the workflow for the corresponding machining step. The system therefore knows which tools are required for which jobs. Thanks to the complete digital recording of all physically available tools in production by EVOMECS, there is full transparency about the tool inventory. This not only includes information about the storage location of the tools, but also about their condition, measurement data and usage times, as well as information about which tool was used for which component. When an order is ready for processing on the machine, the worker is shown which tools are required. Difference lists can be used to filter which tools are still missing, which are in the machine and are required and which are in the machine but are not required for the selected orders and can be removed. The tool information is transferred to the machine control system digitally via the EVOMECS LinkApp, so that no manual and error-prone entries are necessary.
Workpiece
Ideally, the workpiece to be machined is mounted on the machine using a clamping system (pallet). In this case, the workpiece is first "linked" by EVOMECS to the clamping system, which can be identified via a QR code, for example. During this process, the corresponding offset data of the workpiece on the pallet is also transmitted to the system. The pallet with the assembled workpiece is in turn mounted on the machine and "linked" to the machine. The offset data is then transferred to the machine control system. Similar to the tools, the processing-relevant information is also written to the machine control system digitally and without manual and error-prone input. In principle, the assignment and information transfer of the workpiece to the machine also works without clamping devices.
The digital recording of all relevant input requirements via EVOMECS therefore creates the basis for a smooth and reliable machining process. Professional and technically relevant decisions have already been made in advance. As already mentioned, highly qualified personnel can therefore be deployed where these decisions are made, particularly in planning or CAM programming, for example. No special prior knowledge of CNC machining is then required at the machine itself, which on the one hand reduces the number of personnel required, but above all also enables the use of less qualified personnel.
With EVOMECS, you can take the next step towards efficiency, safety and flexibility in your production. Arrange a live demo now and let us show you how EVOMECS can revolutionize your production. Or even easier: test the software free of charge and experience the benefits for yourself!
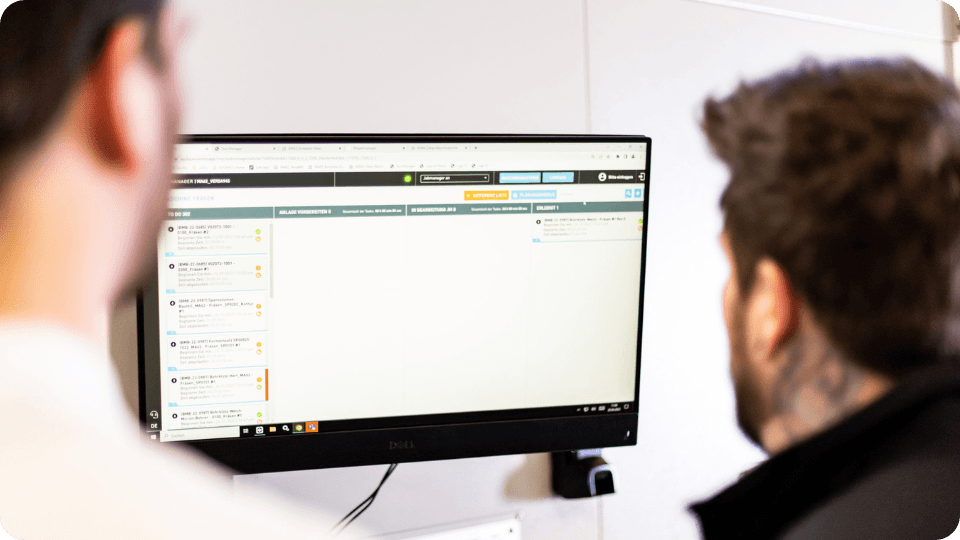
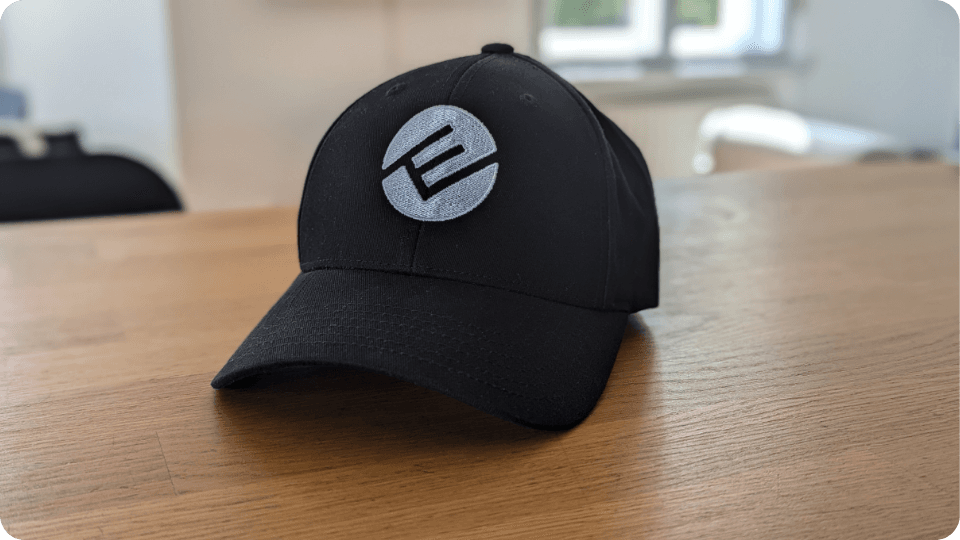
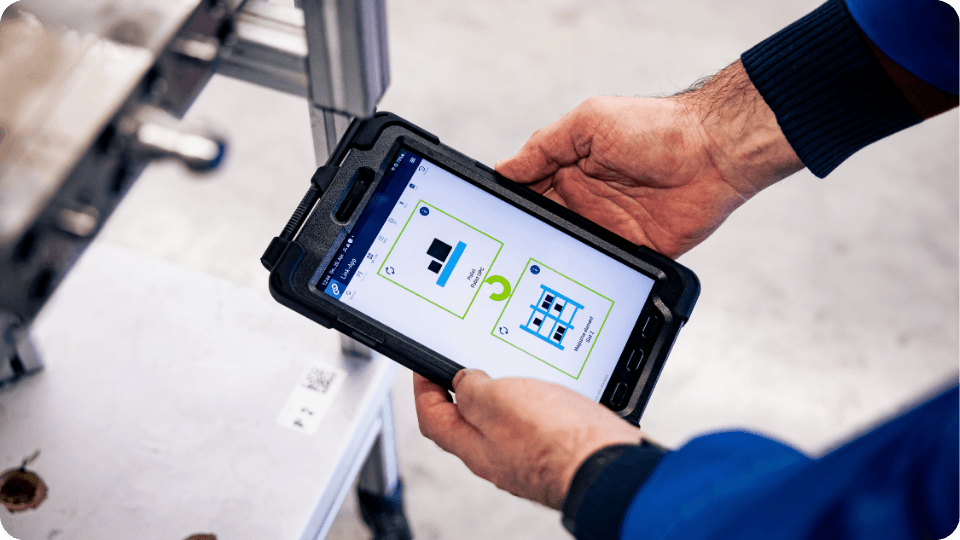